PDCA Cycle – What is it and what can it do?
The PDCA Cycle is a four-step iterative methodology utilized in solving problems, implementing solutions, and fostering change [1, 2, 3, 5]. The “PDCA” in PDCA Cycle stands for Plan, Do, Check, and Act. This methodology is also considered a project management tool that helps improve procedures, processes, products, and services as well as discover new opportunities for ‘change’ to promote continuous improvement [2, 4, 5].
Through PDCA, individuals can team up to develop hypotheses to solve a problem, generate ideas, test and implement potential solutions, and improve upon them in a continuous cycle [6]. This approach has proven versatility in driving organizations to effectively adapt to market changes, improve efficiency, boost productivity, meet customer expectations, optimize business performance, and foster a culture of continuous learning [7, 8, 9].
The PDCA Cycle is valued for its systematic structure and significant contributions to problem-solving, continuous improvement, quality management, and; making it a fundamental component in both Lean Manufacturing and Root Cause Analysis (RCA).
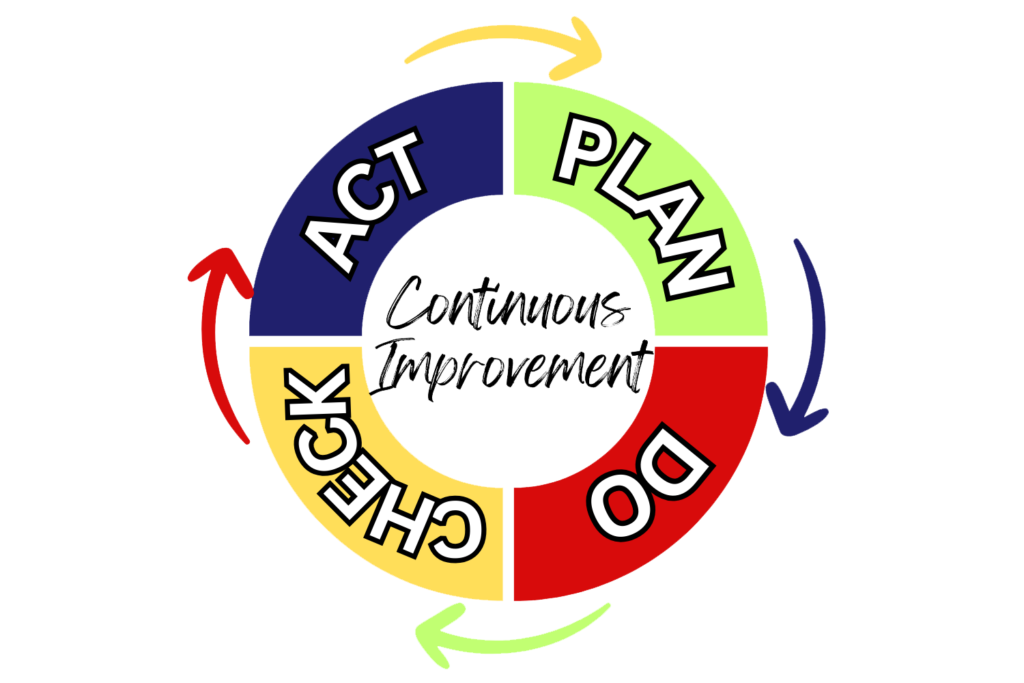
Purpose of PDCA cycle
The main purpose of applying the PDCA approach is to continuously improve processes by defining issues/areas for improvements and facilitating the deployment of positive changes.
Within the PDCA Cycle, significant emphasis is placed on thorough initial planning and the utilization of statistical tools. These tools assist in uncovering issues and enabling the implementation of data-driven interventions [10].
As the name implies, PDCA works in a cycle where solutions are implemented to rectify issues and where improvements can be continuously incorporated to enhance processes through the four stages of Plan, Do, Check, and Act [11]. Likewise, it can enhance problem-solving, decision-making, innovation, adaptability, and quality [7].
When your operations stumble upon a problem or there is a process that is not hitting the target, you can apply the PDCA cycle to solve the problem, improve the process, and innovate more ways for better improvements.
For instance, to overcome an issue, your team can [3];
PLAN | : | set goals against the current baseline of performance and generate potential solutions |
DO | : | test out and implement the best solutions to achieve the goal |
CHECK | : | measure the improvement inspected to evaluate the performance against the target |
ACT | : | standardise the new method by updating the standardised work (once measurable gain is achieved) or redo the project to take corrective actions (if measurable gain is not achieved) |
Brief History of PDCA
The PDCA Cycle has many alternative names including Deming Cycle/Deming Wheel (after W. Edwards Deming) and Shewhart Cycle (after Walter A. Shewhart).
To put it briefly, this approach was first introduced by Walter A. Shewhart – a.k.a. the Father of Statistical Process Control – in the 1920s which was initially a three-step linear approach (Specify-Produce-Inspect) which he then altered into a cycle. This framework was then championed by W. Edwards Deming – a.k.a. the Father of Total Quality Management – and named it the “Shewhart Cycle” (after his mentor). Deming then further developed it into a four-step model (Design-Produce-Sell-Research) when he popularised it to the public within the field of Total Quality Management, mostly Japanese audiences, and was renamed the Deming Cycle/Deming Wheel. This approach was later further modified into the current Plan-Do-Check-Act (PDCA) Cycle framework [3, 4, 6, 7].
The PDCA Cycle was initially applied as a means for quality-checking of products. However, as it gained popularity, it was further developed into a framework that extends into developing improvements in processes and operations at an organizational scale. Now, the PDCA cycle is renowned for fostering a culture of continuous improvement and as a framework that enables improvements in operations and activities [1, 9].
How to Apply PDCA Cycle
Now that introductions are made about the PDCA Cycle and when it can be applied. You and your team can start to execute it!
As stated, the PDCA Cycle consists of Plan, Do, Check, and Act that work sequentially with each stage bearing different functions (as their term entails). The below illustrates a summary of what you need to do at each stage of the model;
For a more detailed way of executing it, the steps to implement the four stages of PDCA are outlined below [1-7, 9];
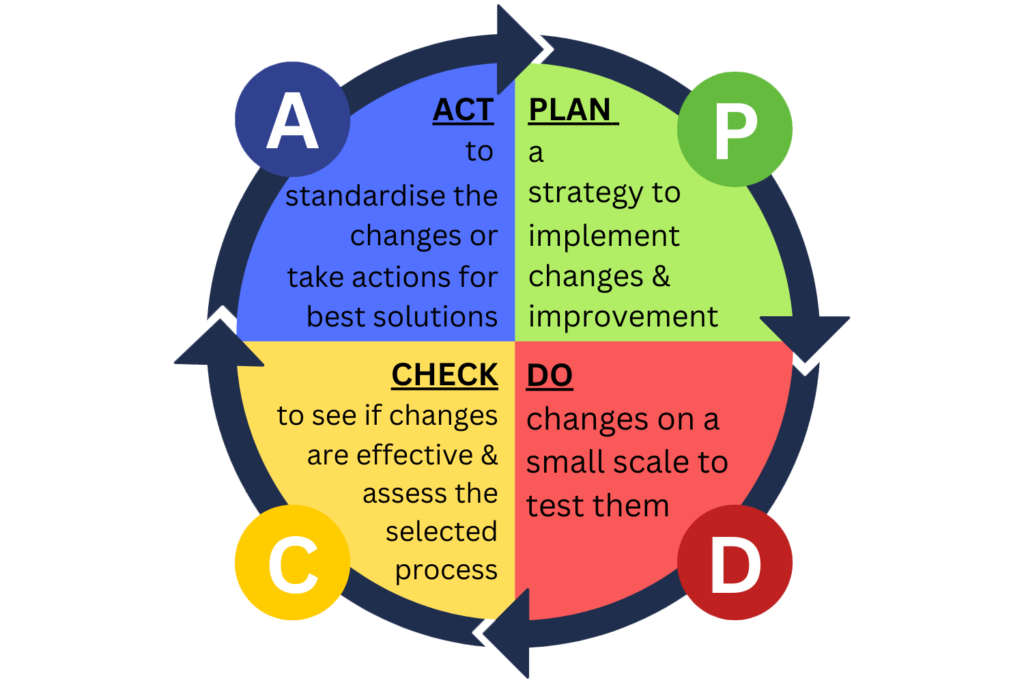
Steps To Implement The PDCA Cycle
P – Plan
1. Identify the opportunities/issues
- Clearly define the goal of the project by determining issues or areas for improvement (e.g., product standards, process improvements, or service quality)
- Find the scope of the issue/area for improvement and break it down into different categories
- Prioritise high-impact issues/areas for improvement
2. Identify the root cause of the issue defined
- Conduct a root cause analysis (RCA) to determine the root cause of the issue/need for improvement
- Apply RCA tools and techniques to accurately detect the root causes. Eg., 5 Whys, Fishbone Diagram, etc.
3. Capture and evaluate the current standard/performance of the products, processes, or services
- Gather data on their current performance
- Visualise the data for easier and faster explanation of the performance
4. Set targets/objectives
- Once the goal is defined, set SMART (specific, measurable, attainable, relevant, and time-bound) targets to be achieved
5. Establish robust planning
- Formulate a clear project plan that aligns with organizational goals to achieve the targets
- Assign tasks and roles/responsibilities among team members, set schedules and deadlines, and determine the resources needed, risks, and constraints
6. Propose potential actionable plans
- Generate ideas and brainstorm possible actionable plans that can solve the issue or improve the areas
D – Do
1. Develop actionable plans and potential solutions
- Brainstorm with team members to develop potential solutions
- Select the best solutions to implement
2. Implement changes and conduct a small-scale test or pilot project
- The test/pilot project allows for safe testing to determine if proposed changes yield the intended results while minimizing disruption to the overall operation (if adjustments are needed)
3. Gather data and document unexpected events and lessons learned
- Record unexpected events, lessons learned (positive & negative), and acquire knowledge for comprehensive implementation and documentation of the action plan
C – Check
1. Gather the results from the pilot project/test
2. Conduct a comprehensive result analysis and review the outcomes
3. Assess the effectiveness of the proposed changes
- Conduct a before and after comparison between the initial performance/standard with the one after the pilot project/test to confirm if there have been improvements and if the targets were met
- Provide data visualisation of the comparison
A – Act
1. Based on the results obtained in ‘Check’;
- If the targets have been reached: develop methods aimed to standardize the improvements. The proof is repeated to obtain new data and re-test the improvement (only if data are insufficient or circumstances have changed),
- If the project does not meet the targets: reinitiate a new project from the first stage, take corrective actions, and make adjustments to achieve the targets
2. Set a new goal and initiate a new cycle to set higher standards and make better improvements to foster continuous improvement
When to Use PDCA Cycle
The PDCA Cycle is a universal improvement tool that can be applied in multiple kinds of industries (manufacturing, healthcare, service providers, etc.) and projects to improve any process, product, or service [1]. It also works very well in routine management and inventory management as well as in the field of Total Quality Management (TQM). PDCA can also be integrated with other improvement methodologies such as the A3 Report and Lean Six Sigma for a more detailed approach [1, 7].
Essentially, PDCA is applicable in any process and enables your organization to work continuously to improve the quality of your business standards and productivity [7].
So, whenever you are working on [1, 6];
- starting a new improvement project,
- resolving recurring problems,
- product/service quality management,
- streamlining and improving repetitive work processes,
- implementing change and continuous improvement in your daily work routine, or
- developing a new design of a process, product, or service,
Then, you can always round up your team to utilize PDCA, brainstorm possible solutions and improvements, and implement them within your organization.
Benefits of Utilizing the PDCA Cycle and Its Impact on Industries
The PDCA Cycle has proven to be a powerful tool with numerous positive outcomes; contributing to the flourishing growth of renowned companies such as Nestle, Lockheed Martin, Toyota, and Nike.
On top of that, the PDCA Cycle has become a key component in implementing ISO (International Organization of Standardization) standards for quality management (ISO 9000) – specifically the ISO 9001 Quality Management System (QMS) standard. It aligns with the requirements and objectives of ISO 9001 as it helps organizations to systematically determine and address issues in their processes, monitor and measure their performance, and continuously improve their QMS [14, 15].
Continuously going through the four stages can facilitate task management and increase product and service value. Hence, your organization’s working environment becomes more productive, processes are more optimized, and bottlenecks are easier to identify and address [7].
Not only does it help address, analyse, and resolve organizational issues; but it can also enhance your organization’s internal and external processes. For instance;
- Help organizations get started with continuous improvement,
- Provide a systematic approach to improve any processes, products, and services and resolve problems,
- Boost productivity and foster dynamic teamwork through regular brainstorming sessions and discussions,
- Reduce risk and encourage testing out possible solutions on a small scale within a controlled environment,
- Prevent recurring mistakes and errors,
- Optimize resources and reduce waste,
- Save and optimize costs,
- Enhance customer satisfaction.
From these benefits, PDCA can significantly bring positive impacts to an organization. As this approach mainly focuses on problem-solving and continuous improvement, multiple industries can obtain fruitful outcomes.
For example, through the PDCA Cycle approach, the manufacturing industry can improve production efficiency, optimize the supply chain, and reduce the number of defects. On the other hand, service providers like hotels, banks, restaurants, and so on can enhance product and service quality, improve quality management, and reduce waiting time which ultimately can meet customers’ needs and increase customer satisfaction. In addition, the education industry can also employ the PDCA approach to refine teaching techniques, enhance and adapt the curriculum, and elevate the academic achievements of students whereas the healthcare industry can reduce the turnaround time, enhance healthcare quality, minimize medical errors, and optimize workflows.
What is The Relationship Between PDCA and DMAIC?
The PDCA Cycle holds a strong similarity with the renowned improvement tool; DMAIC Methodology. For instance [12, 13];
- Both PDCA and DMAIC function as problem-solving tools,
- Both PDCA and DMAIC aim to improve quality and efficiency,
- Both PDCA and DMAIC employ both quantitative and qualitative research techniques.
- Both PDCA and DMAIC go through a plan, execution, and control phase (despite different terms and number of stages).
Despite their similarities, both the PDCA and DMAIC methodologies have their differences as well, such as [12, 13];
- PDCA is more suitable for straightforward problems while DMAIC is employed to solve complex problems,
- PDCA mostly applies basic statistical tools for analysis while DMAIC uses advanced statistical tools and techniques,
- PDCA is intended for continual utilization to attain a state of continuous improvement, whereas DMAIC is designed to implement purposeful and impactful modifications to tackle challenges for the big picture.
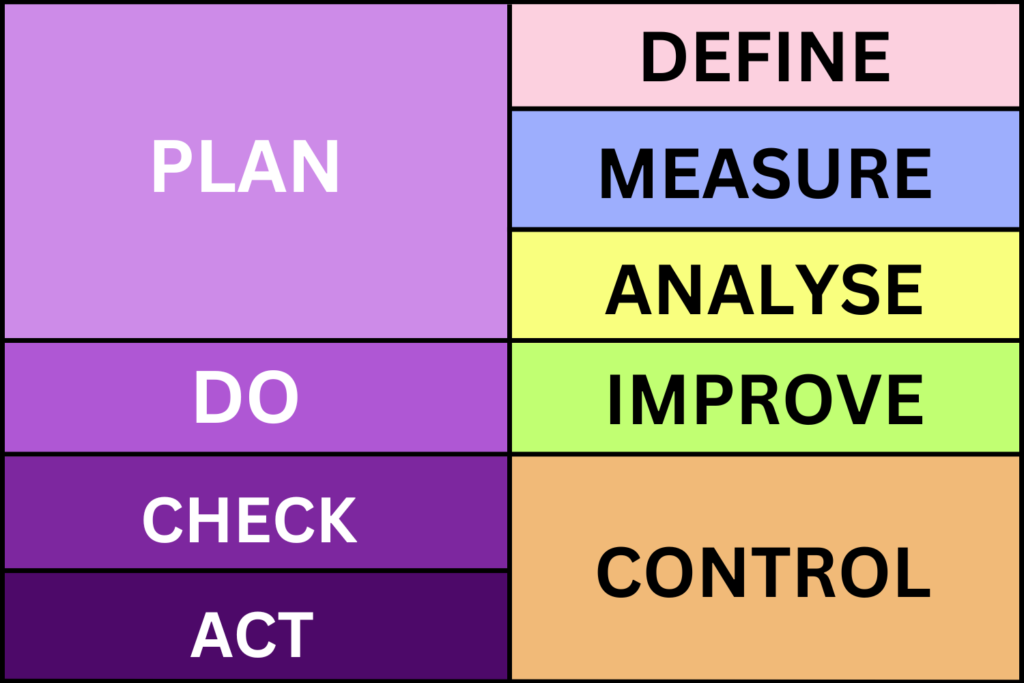
Based on both methods’ principles, DMAIC puts more focus on planning while PDCA puts more focus on evaluating results and implementation. The graphic above visualizes how these methods have different emphases in their approaches.
DMAIC puts three stages (Define, Measure & Analyse) in PDCA’s Plan stage, On the other hand, PDCA puts more focus on evaluating results and implementation as shown above where it has two stages (Check & Act) in DMAIC’s Control stage.
In brief, choosing which methods to deploy highly depends on one’s expertise in the field of process improvement and one’s competence in utilizing its tools as well as the complexity of the process or issues that require improvement.
In conclusion, the PDCA cycle stands as a dynamic and proven method for continuous improvement in processes. This continuous cycle of planning, doing, checking, and acting provides a straightforward and effective approach to problem-solving and change management.
Notably, its utility lies in the ability to test improvement measures on a smaller scale before implementing broader changes, ensuring a strategic and iterative path to success. Beyond its practical applications, the PDCA Cycle fosters a transformative cultural shift in businesses, encouraging input from all stakeholders who can actively contribute as problem-solvers and critical thinkers. This, in turn, cultivates a rich environment for generating innovative ideas and driving positive change.
Interested in deploying the PDCA Cycle in your organization? Hit us up!
If you are interested in deploying this powerful methodology to improve your business processes and foster continuous improvement, come visit us at https://leansixsigma.com.my/ for more information, or you can fill in your details and inquiries at https://leansixsigma.com.my/contact/ and we will help you get started.
Ready to enhance your process efficiency and conquer challenges? Our seasoned experts are here to help kickstart your journey – reach out today and let’s make a difference together!
Need training?
Then, come and enroll in our Lean Six Sigma training now and learn the methodologies and techniques to increase profitability through waste elimination, quality management, and continuous improvement!
Choose your preferred training mode here; public training, in-house training, and online training.
Be a member today!
Join us and become a member to receive various membership perks – vouchers, discounts, networking, and more! Visit us at https://sixsigma.org.my/membership/ for more information.
Looking forward to having you onboard!
Follow MBizM Group channel on WhatsApp and get the latest updates on Lean Six Sigma facts and training programmes!
REFERENCES
- “PDCA {Plan Do Check Act},” MindTools, https://www.mindtools.com/as2l5i1/pdca-plan-do-check-act (accessed Jan. 24, 2024).
- “PDCA Cycle – What is the plan-do-check-act cycle? | ASQ,” American Society for Quality , https://asq.org/quality-resources/pdca-cycle (accessed Jan. 24, 2024).
- “Plan, do, check, act (PDCA) – A Resource Guide,” Lean Enterprise Institute, https://www.lean.org/lexicon-terms/pdca/ (accessed Jan. 24, 2024).
- M. Hargrave, “What does PDCA stand for in business? plan-do-check-act cycle,” Investopedia, https://www.investopedia.com/terms/p/pdca-cycle.asp (accessed Jan. 24, 2024).
- “PDCA cycle,” What Is the PDCA Cycle? | Definition and Overview, https://www.productplan.com/glossary/pdca-cycle/ (accessed Jan. 24, 2024).
- J. Martins, “What is the Plan-Do-Check-Act (PDCA) cycle?,” Asana, https://asana.com/resources/pdca-cycle(accessed Jan. 24, 2024).
- “PDCA Cycle: What are the stages and how does it work? See examples,” Sydle, https://www.sydle.com/blog/pdca-cycle-61ba2a15876cf6271d556be9 (accessed Jan. 24, 2024).
- A. Prashar, “Adopting PDCA (plan-do-check-act) cycle for energy optimization in energy-intensive smes,” Journal of Cleaner Production, vol. 145, pp. 277–293, 2017. doi: http://dx.doi.org/10.1016/j.jclepro.2017.01.068
- A. Realyvásquez-Vargas, K. Arredondo-Soto, T. Carrillo-Gutiérrez, and G. Ravelo, “Applying the Plan-Do-Check-Act (PDCA) Cycle to Reduce the Defects in the Manufacturing Industry. A Case Study,” Applied Sciences, vol. 8, no. 11, p. 2181, Nov. 2018. doi: http://dx.doi.org/10.3390/app8112181
- S. D. Morgan and A. C. Stewart, “Continuous improvement of team assignments: Using a Web‐based tool and the plan‐do‐check‐act cycle in design and redesign,” Decision Sciences Journal of Innovative Education, vol. 15, no. 3, pp. 303–324, 2017. doi: https://sci-hub.se/https://doi.org/10.1111/dsji.12132
- Nabiilah, A. R., Hamedon, Z., & Faiz, M. T. (2018). Improving quality of light commercial vehicle using PDCA approach. Journal of Advanced Manufacturing Technology (JAMT), 12(1 (2)), 525-534.
- “PDCA vs. DMAIC: What’s the difference?,” isixsigma, https://www.isixsigma.com/dmaic-methodology/pdca-vs-dmaic-whats-the-difference/ (accessed Jan. 24, 2024).
- M. Cancian, “PDCA vs DMAIC: Which one should you use?,” Think Lean Six Sigma, https://www.thinkleansixsigma.com/article/pdca-dmaic (accessed Jan. 24, 2024).
- V. Hyseni, “The plan-do-check-act (Pdca) cycle: A guide to continuous improvement,” PECB, https://pecb.com/article/the-plan-do-check-act-pdca-cycle-a-guide-to-continuous-improvement (accessed Jan. 30, 2024).
- “ISO 9001:2015,” ISO, https://www.iso.org/standard/62085.html (accessed Jan. 30, 2024).